پڕۆفایلە کۆنجداری ئەلومینیۆم یەکێک لە زۆر بەکارهاتووترین پڕۆفایلە ئەلومینیۆمییەکانە. بوونی پڕۆفایلە کۆنجداری ئەلومینیۆم لە ناوەڕاستی سەدەی بیستەوە لەگەڵ پەرەپێدانی تکنەلۆژیی بەرهەمھێنانی ئەلومینیۆم و بەرتووکایەکیی نرخی بەرهەم بە شێوەیەکی بەرچاو زیادبووە.
. Among the features that distinguish aluminum corners are their light weight, corrosion resistance, and flexibility. The cross-section of an aluminum corner is similar to the letter “L”, which consists of two wings with a 90-degree angle, and the length of both wings can be equal (equal) or unequal (unequal). The standard size and dimensions with two factors “wing length and thickness” of the aluminum corner from 12 mm to 160 mm with different thicknesses are available in the market depending on the application in industries
Aluminum Corner Profile Manufacturer
AlumLand Industrial Group, with its third-generation production line, has the ability to produce various types of aluminum profile sections on a mass scale and at the "lowest price". Buying aluminum corner profiles directly from Alum Land Company, one of the largest manufacturers of aluminum profiles, allows you to buy at a cheaper price and with fast delivery. We assure you that our products have the best quality and standard and will meet all your expectations
Price inquiry : 09123794374
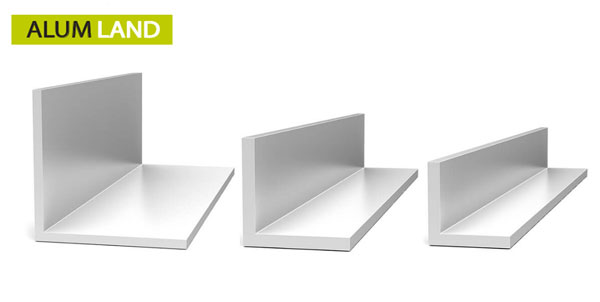
Aluminum Corner Price
The price of aluminum corners produced by Alum Land Company depends on the order and is in branches and bulk depending on several main factors, including:
Type and alloy used in the production of corners: the type of aluminum used, whether it is new or recycled, and the type of alloy
The daily price of billet (aluminum profile price) or aluminum sheet: global price fluctuations, decrease or increase in consumption
Weight, thickness, and dimensions of the corner: the thicker and larger the dimensions of the corner, the more material is consumed and the weight of the corner increases
Production process: the production method affects production costs
Type of processing and finishing operations: anodizing, coating, painting, and polishing can also have a direct impact on increasing the price
Order quantity: the higher the order quantity, the lower the price.
Dimensions of Aluminum Corner
Aluminum corners are available in the market in standard sizes and based on two factors, wing length from 10 x 10 mm to 200 x 200 mm, and in terms of thickness, in three categories: thin from 1 to 2 mm, medium thickness from 3 to 6 mm, and thick from 7 to 10 mm, and buying these sizes according to the need can be cost-effective, and if needed or special applications, the desired size and thickness can be custom-made, which usually requires more cost and time
Guide to Buying Aluminum Corner
When buying aluminum corners, be sure to pay attention to the following points:
Corner weight: the higher the weight and dimensions of the aluminum corner, the more load and weight it can bear, so choose the type of corner according to the needs of the project
Corner thickness: usually, thick corners are used for places or structures that are exposed to environmental factors such as humidity. Therefore, you should pay attention to the type of application when choosing the corner thickness.
Corner alloy type: the quality of the material has a significant effect on the durability of the corner. When buying, be sure to pay attention to the rust or corrosion of the corner
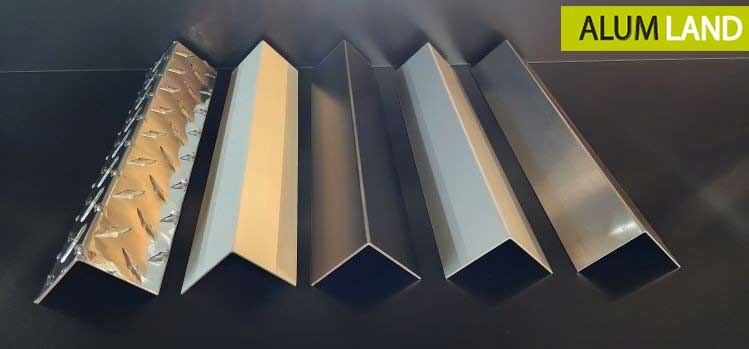
Types of Aluminum Corner
Aluminum corners can be divided into two categories, light and heavy, in terms of weight, and into two categories, thin and thick, in terms of thickness, or in terms of shape and performance:
Standard corners (L-Shaped Angles) which are divided into two categories: equal leg angles – unequal leg angles, which are mostly used in construction, strengthening structures, and framing doors and windows.
T-shaped angles, which are in the shape of the letter T, are made of a combination of two L-shaped corners and are used in the construction of bridges, heavy structures, and special industrial applications.
U-shaped channels are in the shape of the letter U and have three wings and are used in the construction of window frames, doors, and structural reinforcements.
Method of producing aluminum corner
Extrusion method
One of the most common methods of producing and manufacturing aluminum corners is aluminum extrusion, which in short, in this method, the heated aluminum billet (ingot) is passed under pressure in an extrusion press through an extrusion die to produce the desired section and shape. This method is used to produce aluminum corners with a specific section and size in mass production and allows complex forms with high accuracy and high surface quality.
AlumLand Company, with its third-generation aluminum profile production line and extrusion press, produces aluminum corners based on orders and in a wide range of alloys, sizes, and thicknesses with the best materials and the highest quality and compliance with global standards on a mass scale.
Rolling method
In the rolling process, aluminum sheets or strips are bent under pressure using rollers to produce a corner with the desired angle and shape, and it is mostly used to make aluminum corners with simple sections. Among the advantages of the rolling process, we can mention speed and economic efficiency.
Casting method
In this process, molten aluminum is poured into a mold and after cooling, it is removed from the mold to make an aluminum corner with the desired shape and angle. This process is more suitable for making and producing aluminum corners with irregular angles and shapes, although it is less used than the extrusion method due to its lower production speed, but the advantages of this method are lower cost and production of complex or irregular shapes.
Types of Aluminum Corner Alloys
Alloy 6061 due to the good balance between strength and flexibility and excellent properties such as: high tensile strength (45000 psi), yield stress or yield strength (40000 psi), high machinability and good weldability (weldability) is widely used in heavy structures and parts of aerospace structures.
Alloy 6063 is another widely used option in the manufacture of aluminum corners. Alloy 6063 with a smoother and smoother surface than other alloys is a good option for applications where beauty and appearance are important, such as decoration and architecture. Extruding alloy 6063 into complex shapes is very easy. The properties of this alloy: high tensile strength (27000 psi), yield stress or yield strength (21000 psi)
Aluminum 5052 contains magnesium as the main alloying element along with traces of chromium. One of the characteristics of this alloy is its high resistance to corrosion and rust