Aluminum Profile Production with Extrusion Process
The use of the aluminum extrusion process in the production of aluminum profiles has grown significantly worldwide, with the global aluminum extrusion market experiencing a 4% annual growth rate. In addition to being economical and reducing production costs, the aluminum extrusion process does not create limitations in the production of shapes and sections and allows the production of special and complex sections and shapes.
d.
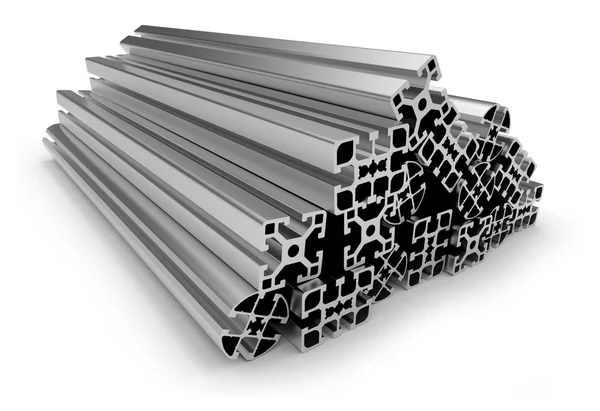
Alumland Industrial Complex, a producer of various types of aluminum profiles, equipped with a new generation of aluminum profile production line (extrusion press) and an experienced team of engineers, has made it possible to design and manufacture all kinds of aluminum profiles in all stages from making the extrusion die to anodizing and electrostatic powder coating services while maintaining the highest level of standards. We have the construction of 900 exclusive dies in our record
The process of producing aluminum profiles
Due to its many advantages, the extrusion process is considered the best method for producing aluminum profiles. The extrusion press allows the production of all kinds of aluminum sections with different shapes and different applications with high accuracy
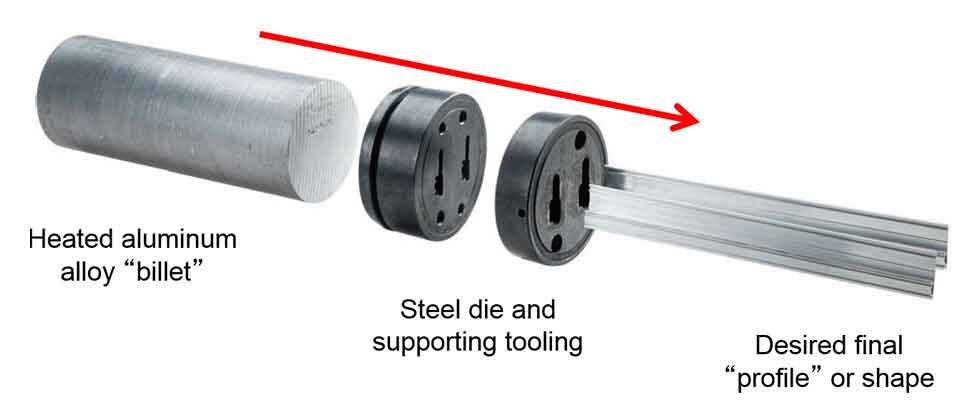
In the process of producing aluminum profiles by the extrusion process, the aluminum billet, after being heated (250-500 degrees Celsius), is moved under very high pressure through special dies, and thus, due to the application of the heat and high pressure process on the aluminum metal, the raw material is completely changed. It is formed and finally, the aluminum profile or the desired section is produced
Stages of aluminum profile production
The production of aluminum profiles by the extrusion process includes the following steps
Designing and manufacturing the aluminum profile production die
It includes the initial design of “dimensions, shape, thickness, and other technical details” and technical analysis of the desired section based on the needs and performance, based on which the design and construction of the die is done.
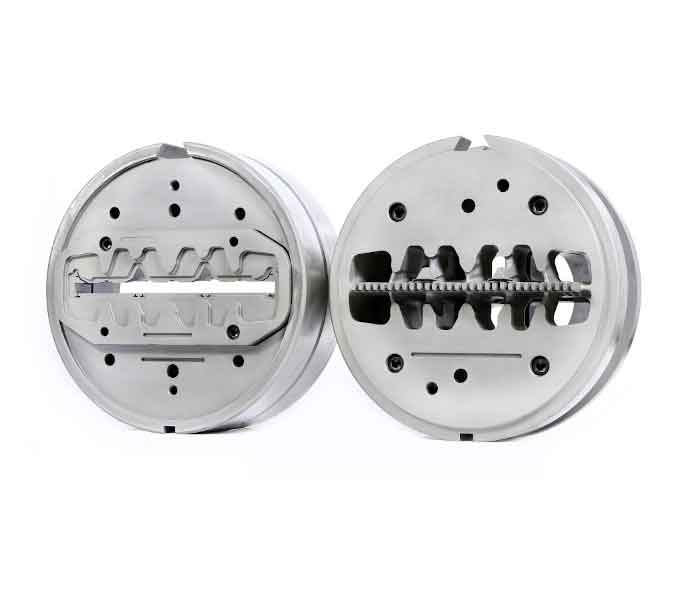
Extrusion die
The aluminum profile production die is used in the extrusion or casting process to shape the aluminum billet in the desired dimensions and sections. Alloy or stainless steel is used to make the extrusion die because these types of materials have resistance and tolerance to high pressure and temperature. The aluminum profile production die (extrusion) consists of two parts: the main die, which shapes the form and structure of the aluminum profile, and the shaping die, which plays a role in determining the details of the section.
The steps of making an extrusion die include:
Die design: Using 3D modeling software such as SolidWorks or AutoCAD, the specialists and engineers of Alumland Company design the extrusion die based on the needs and performance of the custom aluminum profile and the type of material considered.
Die making: After being designed, the dies are made by CNC machines and precision machines of the Alumland complex.
Testing and adjustments: In this stage, the specialized team of Alumland tests the dies and makes the necessary adjustments to optimize the production process
Selection of raw materials (billet)
The required raw materials are selected based on the needs and performance for making the aluminum profile. This includes determining the standard of pure aluminum and additives such as various alloys, lubricants, and coloring materials
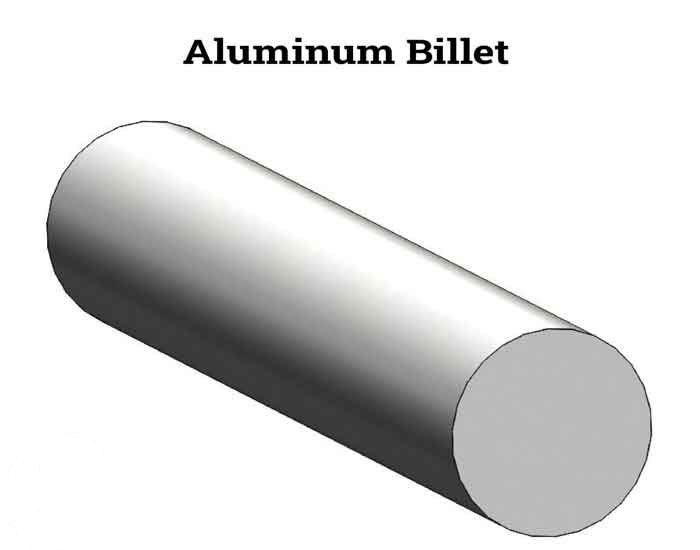
Factors to consider when choosing raw materials include: formability or workability, weldability, machinability, corrosion resistance, heat treatment, strength and power, final use and applications.
Aluminum alloys are known based on their composition and properties with four-digit codes (the first digit indicates the class or series of the alloy), such as: 4xxx, 6xx.x and 2xxx. For example, for the production of aluminum door and window profiles, alloys of the 6xxx series such as 6060 and 6063 are suitable due to their good formability, weldability, machinability, and high corrosion resistance.
Aluminum profiles are produced using aluminum alloys of groups (6xxx such as 6063, 6101, 6201, etc.) as well as other aluminum groups such as (2xxx, 7xxx, etc.) and delivered according to the customers’ wishes. The produced profiles are classified into categories called temper, considering the mechanical and thermal properties desired by the customer and national and international standards, and according to the type of temper, the production lines have their own special settings
Extrusion process
In this stage, the aluminum billet passes through special dies (usually dies with a specific shape) under pressure, as a result, the cross-section of the extruded profile will be in the shape of the same output hole, and in this way, the aluminum is formed into the desired profile with precise dimensions and different shapes. The extrusion process can be divided into two categories, direct and indirect, based on the direction and type of pressure applied.
Indirect extrusion
In the indirect extrusion method, unlike the direct method, the moving die moves towards the aluminum billet. In this method, the direction of movement of the punch is not aligned and opposite to the product, and in fact, the die is pressed into the molten aluminum billet, which is inside a closed chamber, and as a result, it leads to the formation of the aluminum profile. In this method, there is less friction and as a result, less heat is also produced. This method is mostly used for the production of aluminum profiles with special applications.
Direct extrusion
In the direct extrusion method, the aluminum billet is injected into the die from the back with the help of a punch. In this direct process, the die is fixed and the punch (ram) moves in the same direction as the product output. In this method, high friction (contact of the aluminum billet with the die wall) leads to the production of a lot of heat. In this method, more energy and force are needed compared to the indirect method, however, the direct extrusion method is the most common method in the production of aluminum profiles.
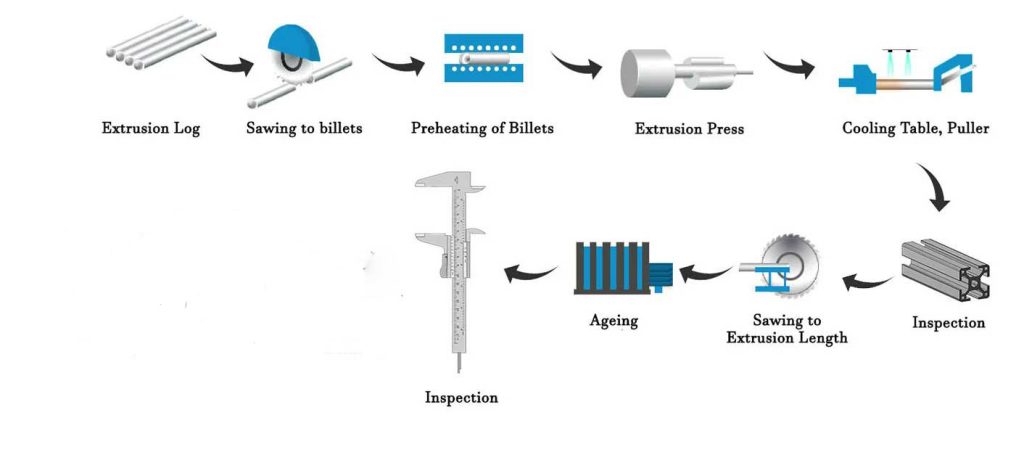
Cutting, cooling, and post-process operations
The made aluminum profiles must be completely cooled and then go to the next stage of post-process stages, which includes cutting, removing unnecessary programs, strengthening and correcting the final dimensions of the profile.
One of the advantages of direct extrusion is the ability to control and cool the extruded part after it comes out of the die, which after cutting, the product is guided to the cooling table, after the aluminum cools and moves along the cooling table, the hardening and stretching stage of the extrusion increases the hardness of the aluminum profile and increases the strength.
Coating and finishing
In this stage, depending on the type, production scale, and special needs of aluminum profiles, it can include anodizing, coating, and painting.
Advantages of the extrusion process
The production of aluminum profiles through the extrusion process allows the manufacturer to design and produce aluminum profiles with different sections and shapes with high accuracy and quality. Among the advantages of the extrusion process, we can mention:
It has made it possible to produce aluminum profiles in various shapes and dimensions with complex forms and precise sizes. For this reason, quality products with different functions in different industries can be obtained.
The low weight and lightness of the aluminum profile produced by the extrusion process make them suitable for use in various industries such as construction, aerospace, and automotive.
The aluminum profile produced by the extrusion process has high resistance to corrosion and therefore is suitable for use in outdoor environments or high humidity.
The recyclability is another important feature of using the extrusion process in the production of aluminum profiles, which can increase the economic efficiency of this cycle.
The extrusion process allows the production of all kinds of sections and designs without limitation, for this reason, products with high aesthetic appearance can be obtained.
Your trust is our distinguishing feature
Alumland Industrial Complex, with years of experience in the production of aluminum profiles and the construction of hundreds of extrusion dies, has been able to take a big step towards quality production. Alumland, using specialized personnel and a quality control unit and using standard materials, offers various sections of aluminum profiles with the highest possible quality to the market Alumland factories have the ability to produce all kinds of aluminum profile sections in bulk and completely exclusively based on the customer's order in the shortest time and at a reasonable price
Price inquiry : 09123794374
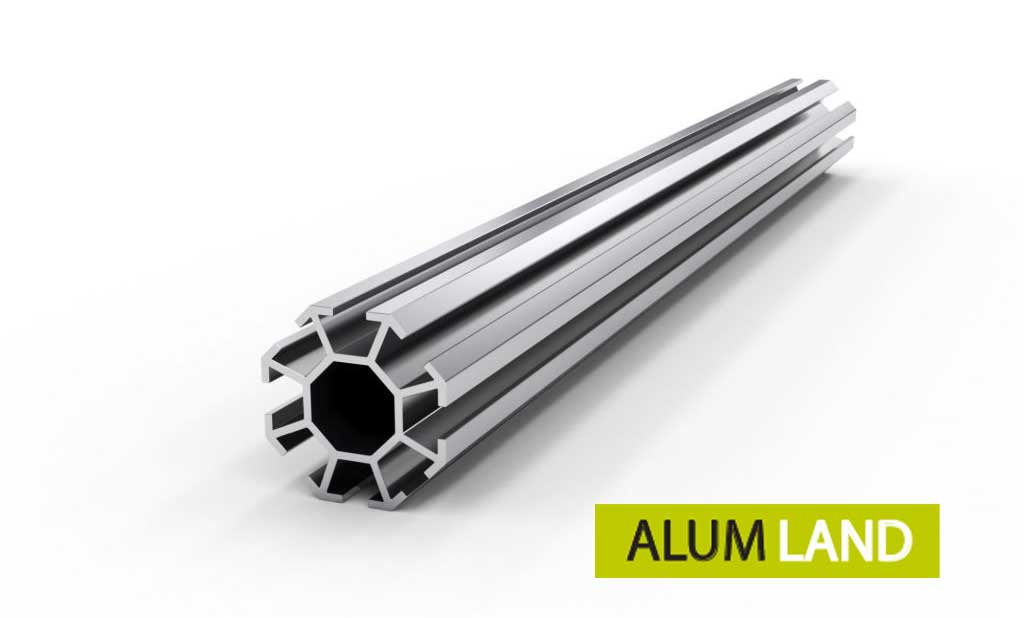
Aluminum profile production line
Alumland Company, equipped with an aluminum profile production line and an aluminum billet production line, is capable of producing all kinds of aluminum profile sections and all kinds of aluminum billet alloys.
Devices of the aluminum profile production line
The standard of Alumland Company, which includes: billet preheating furnace, die preheating furnace, extrusion press, front table, hot saw, drawing table, buffer table, stretching line, cold cutting table, aging furnace, solution furnace, caustic furnace.
Standard of aluminum profile production
Alumland Company, by complying with the standard compiled by the Institute of Standards and Industrial Research of Iran with number 2384 dated 11/7/62, stating the hardness of at least ten degrees Webster and a maximum of sixteen degrees Webster and the amount of thickness of the plated layer of at least ten microns and a maximum of fifteen microns and the consumed ingot with ALMgSi-0/5 standard and using the chemical composition and physical properties listed in the tables compiled by the Industrial Standards 1 Institute, makes every effort to produce a quality product